Modern repair and remanufacturing techniques can extend the life of worn wind turbine components. The difference lies in the depth and scope of the process applied to the components.
Repair typically involves fixing or replacing specific faulty parts to restore a component to working condition. This is often a less invasive process that addresses immediate issues without fully restoring the component to like-new status.
Remanufacturing is a more comprehensive process where a component is completely disassembled, inspected, and rebuilt, often replacing multiple worn parts and restoring it to original or even improved specifications. This process extends the component’s lifespan significantly, making it nearly as good as (or better than) a new one.
A worn-out main shaft doesn’t mean game over
The main shaft is one of the hardest-working parts of a wind turbine. It carries the weight of the blades, transfers energy to the gearbox, and withstands massive amounts of force. Over time, wear and tear are inevitable as corrosion, misalignment, and bearing seat damage start creeping in.
Many operators assume that once a main shaft shows signs of damage, it needs to be replaced. This means long lead times, high costs, and unnecessary downtime. The reality is that most main shafts can be repaired.
With precision machining, surface treatments, and targeted upgrades, a worn shaft can be restored to like-new condition. Bearings and seals that have reached their limit can be replaced with higher-quality, more durable options for improved performance. Lubrication strategies can also be fine-tuned to prevent future wear. Additionally, monitoring technology can be integrated to track performance in real time, aiding in the early detection of wear and supporting proactive maintenance.
When over and undersize solutions make sense
Wind turbine gearboxes and main shafts rely on tight-fitting bearings to function properly. However, as components wear down over time, bearing seats and housings can lose their original dimensions, leading to increased clearance, misalignment, and premature failure. Instead of replacing an entire housing or gearbox, engineers can apply oversized or undersized bearings to restore a precise fit.
One of the most effective methods for repairing worn bearing seats is thermal spraying. This technique involves applying a new layer of material, typically a metal-based coating, to the damaged surface. The layer is then precision-ground to match the required dimensions, allowing for the use of oversized bearings that accommodate the repair. In cases where a bearing seat is too tight due to material buildup or deformation, undersized bearings can be used after careful machining of the housing.
Why replace bearings when you can remanufacture them for less?
For decades, worn wind turbine bearings were simply thrown away and replaced with new ones. Remanufacturing is changing the game by making it possible to restore and reuse existing bearings at a fraction of the cost.
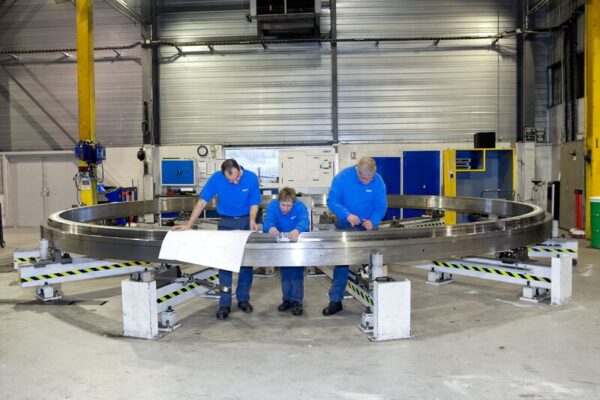
The process is simple. First, the bearing gets a full inspection. If it is only lightly worn, a little polishing is all it takes to bring it back to life. If the damage is more advanced, individual components such as rollers, cages, or seals can be replaced. If a bearing is beyond saving, it is responsibly recycled so nothing goes to waste.
Remanufactured bearings perform just as well as brand-new ones. This process helps cut down on lead times, lower maintenance costs, and reduce environmental impact by keeping tons of metal out of landfills.
Remanufacturing also allows for engineering upgrades. Treatments such as black oxidizing improve corrosion resistance, while specialized heat treatments increase durability. This means remanufactured bearings do not just match the originals; they can outlast them.
Smarter solutions for longer-lasting fleet
Just because a wind turbine component shows signs of wear does not mean it needs to be replaced. With advanced repair and remanufacturing techniques, many parts can be restored to like-new condition, reducing costs, cutting downtime, and extending the life of your equipment.