Politicians are increasingly turning to wind energy to reduce reliance on other countries and simultaneously reach global climate goals. Yet rising energy and material costs, not to mention supply chain disruption, are proving to be stumbling blocks for manufacturers.
It could be that major wind industry players need to develop partner ecosystems to catalyze the energy transition. Only in this way can they ensure the widespread adoption expansion that Europe ultimately longs for. Is it for that reason that this trend of partnering up became a focal point of WindEurope in Bilbao.
SKF played a unique role at the event, sharing its product and service portfolio via on-site touchscreens. Visitors were able to scroll through the presentations at their own pace and discover future solutions.
Why partner up?
The ability to reduce costs, improve profitability, prolong equipment service life, and increase sustainability are just a few of the challenges the wind industry is facing in the modern era of wind energy. This only accentuates the need for high-quality engineering components – and complementary services – that are tailored to their individual demands.
SKF provides exactly the expertise and product portfolio to support the industry as operators, owners, and manufacturers look to continually upgrade turbine performance, and the offerings at WindEurope are evidence of that:
Monitoring turbine condition, loads, and lubrication
- Challenge: 65 percent of maintenance budgets are used for unplanned repairs – the uncertainty of the turbine conditions leads to higher risks and time- and cost-intensive maintenance processes.
- Solution: SKF condition monitoring systems and services and SKF load monitoring measure the individual turbine status. This way, they can predict, alert, and prevent failures, thus reducing unplanned maintenance (costs and time) and enabling data driven decisions.
- Bonus: SKF condition monitoring systems are supported by our global Remote Diagnostic Centers that provide assistance and solutions when questions or emergencies occur.
Lubrication systems
- Challenge: 50 percent of premature bearing damage can be attributed to issues regarding lubrication.
- Solution: SKF automated lubrication systems ensure that parts are greased properly and at the right time. This way, they help increase turbine reliability, reduce unplanned downtime, extend repair intervals, reduce costs, and improve profitability.
Main shaft seals
- Challenge: Low-quality main shaft seals lead to leakage and contamination. On top of that, manual seal exchange is time-consuming and is often performed at lofty heights.
- Solution: High-quality main shaft seals from SKF can improve capability, durability, and performance, while simultaneously extending maintenance intervals and increasing sustainability and value.
Remanufacturing of bearings and lubricants
- Challenge: The wind industry needs to become more sustainable and simultaneously reduce the levelized cost of energy, improve performance, and reduce costs.
- Solution: Remanufacturing is a sustainable solution to reduce CO2 emissions and waste with a positive effect on lead times, and profitability. Additionally, when inspecting bearings during the remanufacturing process, SKF evaluates the bearing’s operating condition and can propose possible upgrades to improve turbine performance.
- Bonus: SKF offers remanufacturing of both bearings and lubrication system components.
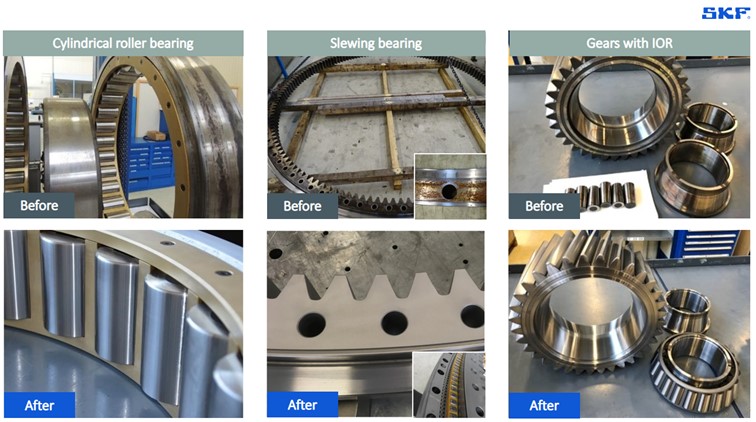
SKF DuraPro for wind turbine gearboxes
- Challenge: Wind turbines are getting bigger and bigger to meet increasing power demand. To keep up with the energy needs and reduce the levelized cost of energy, while ensuring torque density increase and reliability, streamlined turbine components are a must.
- Solution: SKF developed a thermo-chemical process to enrichen and strengthen the surface layer of bearing components. These high-durability bearings are characterized by their prolonged service life, robustness and lower operation and maintenance costs.
- Bonus: SKF was able to downsize these bearings by about 25 percent.
Spare parts management
- Challenge: Missing spare parts drive up maintenance time and costs – especially during an emergency.
- Solution: Research shows that unplanned repairs and missing spares are often the result of unprepared and uninformed supply chain stakeholders. SKF spare parts management stocks the right spare parts at the right place which leads to greater availability and fewer downtime.
- Bonus: The solution is available as standard and can also be customized.
Unlocking the power of data?
- Challenge: Turbine data is siloed and fragmented and it is hard for operators to turn it into something useful. Additionally, it doesn’t provide an overview of the wind turbine’s condition.
- Solution: The SKF Wind Reliability Platform collects, analyzes, visualizes, and communicates data. By combining SKF’s expertise with the wind farm operators’ knowledge, it is possible to make more data driven decisions and increase turbine performance.
Main shaft repair services
- Challenge: Simply replacing a used or broken component does not always solve the problem. Operators need deeper analysis to get to the root cause. On top of that, the overall repairing process is extremely time-consuming.
- Solution: The SKF repair service for wind turbine main shafts is an all-in-one service for wind farm operators that want to mend or exchange turbine components. SKF takes on the dismounting, cleaning, repairing, mounting, and storage and even looks at the surrounding parts to prevent additional failures.
Rising to the occasion?
The industry can only do so much to cope with the latest challenges. Speakers at WindEurope agreed that politicians and decision-makers all over the world need to prioritize the energy transition to minimize the effects of climate change and prevent further damage to our planet. Still, the European wind capacity is 20 percent below the needed installations to meet 2030 emission targets.
To keep up, governments need to simplify the adoption process: They need to negotiate a reduction in energy prices and further expand grids to connect wind farms with energy consumers. We are in for a tough ride – and teamwork could make all the difference. Let’s connect!