Bearings don’t last forever, and their lifespan depends on several factors. Excessive load can cause premature wear due to fatigue, while improper lubrication leads to overheating and accelerated deterioration. Contaminants such as dust, dirt, and moisture can further shorten their lifespan by causing damage over time. Additionally, incorrect mounting can result in misalignment and uneven load distribution, contributing to early failure.
To prevent unexpected failures, operators should watch for these warning signs:
Increased noise and vibration
A healthy bearing operates with minimal noise. If grinding, squeaking, or irregular sounds are detected, this may indicate internal wear or contamination. Vibration monitoring tools, such as vibration sensors, can detect irregularities before they escalate.
Rising operating temperatures
Bearings naturally heat up during operation, but a sudden or sustained increase in temperature suggests inadequate lubrication, excessive load, or misalignment. Thermal monitoring should be a part of routine inspections.
Lubrication issues
Lubrication plays a critical role in bearing longevity. One of the first warning signs of a problem is oil or grease leaks, which can indicate improper sealing or excessive lubricant pressure. Another concern is discoloration of the lubricant, as changes in color can signal contamination or overheating. Excessive grease buildup around the bearing housing may also suggest over-lubrication, which can trap heat and accelerate wear. Regular oil sampling and grease analysis help identify potential failures early and allow for corrective action before significant damage occurs.
Visual damage and wear
Periodic shutdowns provide an opportunity for thorough physical inspections. During these inspections, operators should check for surface spalling or flaking, which indicates material fatigue and impending failure. Discoloration due to overheating suggests excessive friction or lubrication failure. Pitting or indentation caused by contaminants is another warning sign, as debris trapped in the bearing can create stress points that lead to premature wear. If any of these visual indicators are present, replacing the bearing should be a priority to prevent more extensive damage.
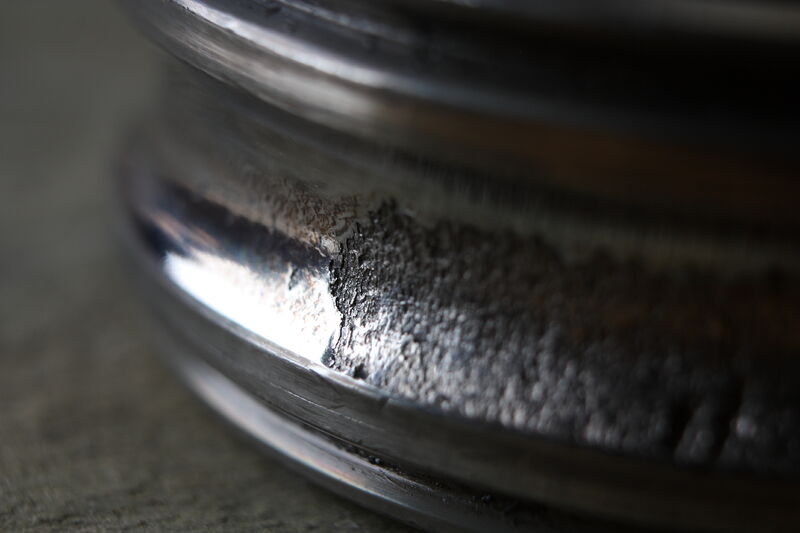
Why proactive replacement matters
Delaying bearing replacement can have serious consequences. A failed bearing can damage not only itself but also nearby components such as shafts and gears, leading to more extensive repairs. Unscheduled maintenance due to bearing failure is disruptive and costly, often requiring extended downtime that affects overall wind farm efficiency. Moreover, the cost of replacing a bearing is minimal compared to the expense of repairing or replacing an entire gearbox or nacelle component. Proactive replacement reduces risks, minimizes costs, and helps maintain continuous operation.
Wind turbine care tips
To maximize bearing life and optimize turbine performance, follow these best practices:
- Implement regular vibration and thermal monitoring
- Use high-quality lubricants and follow manufacturer recommendations
- Apply proper storage and installation techniques
- Conduct scheduled inspections during maintenance shutdowns
Don’t wait for a failure; act on the warning signs early and keep the wind farm running smoothly.