After a number of years of planning and research and development, SKF’s Sven Wingquist Test Center is open for operation. Utilizing a wide range of testing functionalities and technologies, the facility now helps to develop more reliable bearings for the wind power industry, as well as a variety of other sectors.
Software plays a considerable role in the development and testing of large-sized bearings at the test center. At present, engineers use the single-shaft bearing simulation software SimPro Expert for calculating fatigue based on SKF’s extended bearing life theory. In addition to this, the virtual test rig named BEAST is used for simulating the dynamics within a bearing under almost any load condition.
Still progress to be made
However, no software has been able to accurately recreate the complex and unpredictable conditions a bearing goes through in operation. To this extent, current simulation models are somewhat limited. With its advanced testing technology, the Sven Wingquist Test Center could be about to change this. Not only does the site aim to improve the quality of test rigs available, but also to refine the software used in large-size bearing design.
The wind power industry’s very own test rig
Central to the development of new simulation models, are the two giant test rigs. The larger station, sometimes referred to as the main shaft rig, is for testing large-size bearings for wind turbines. Able to transfer significant force through the 7m disc within the rig, the test station exposes bearings to loads across all axes and at increased force. This tests these components under more extreme conditions that were not previously possible to replicate.
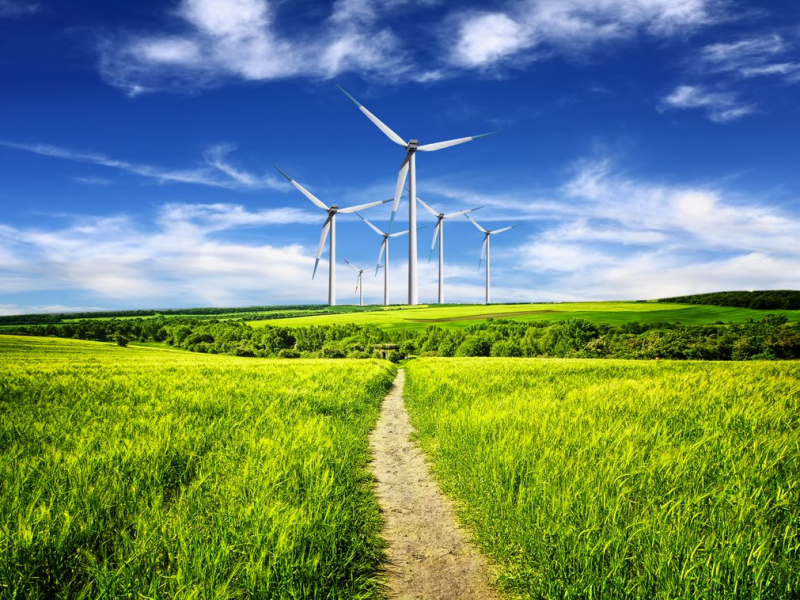
Larger test rig dimensions and features:
- Overall dimension of 9m x 11m x 8m
- Weight of 700 metric tons
- 64 radially and axially arranged cylinders
- Rotating disk with diameter of 7m and weight of 125 metric tons
In addition to the significant forces the large rig can apply, it also speeds up the testing process significantly. With large wind turbine bearings expected to last for at least 20 years, the test station can recreate 20 years of wear within a few weeks. This doesn’t just save time and money, it also saves energy. Furthermore, the heat recovery system uses any generated heat and utilizes it at a nearby bearing factory.
A second test rig for understanding the role of lubrication
While not designed exclusively to test bearings for wind turbines, the smaller station also has an important role to play. Equipped with a specialist lubrication system from SKF, the test rig can lubricate bearings to the optimal level. However, the rig can also apply incorrect lubrication to varying degrees to see how bearings function under different conditions. This provides additional knowledge to designers and engineers that can be used in making bearings more durable.
Smaller test rig dimensions and features:
- 130 metric ton test head
- 4 axial cylinders
- 2 radial cylinders
- Rotational speed of 200 r/min
- Capacity to hold 3,000 liters of lubricant
Moreover, temperature control plays an important role at the testing facility in relation to bearings and lubrication. Designed to expose components to extreme conditions, the smaller test rig can heat lubrication oil to around twice the temperatures encountered in standard testing facilities. The significant range of temperature settings can apply tribological stress to the bearing for more in-depth research.
The future is bright and full of promise
Ultimately, the SKF test center in Schweinfurt is providing the industry with more detailed resources to develop more efficient designs. The extreme conditions components can be exposed to and the greater accuracy of the testing methods will lead to more reliable and durable large-size bearings in the future.