Over the last ten years, the technology integrated in wind turbines has developed rapidly. A key part of these wind giants has always been the rolling bearings: they facilitate the movements of the machine parts and reduce the friction generated in the process. Under heavy external loads, such as uneven and strong gusts of wind, these rolling bearings have to function without problems for at least 20 or in modern designs up to 40 years. Why so long? Because wind turbines are often in remote locations and they tower several dozen meters into the air, making replacing rolling bearings problematic. And in the event of an unplanned failure, considerable costs would be incurred by the wind farm operator, especially for the offshore turbines.
Since the rolling bearings have such a great influence on the functionality of the wind turbine, they must also be perfectly adapted to the conditions in the nacelle, the operating conditions of the turbine, and the design of the gearbox.
Less is more
For some time now, the trend has been toward larger and even more powerful turbines. With reduced reliance on fossil fuels and renewable energies being prioritized politically, the enormous growth in demand for wind power comes as no surprise. But in order to build larger, the turbines have to become lighter. Not an easy task, given the difficult conditions to which rolling bearings are subjected to all while having to retain their robustness, durability, and resilience. Additionally, they need to become smaller and even more reliable so that operators can save costs and increase efficiency.
Larger turbines, smaller components
At the Wind Europe Fair and Conference in Bilbao from April 5th to 7th, SKF will launch a solution to these seemingly conflicting requirements. Bearings made of a new steel and heat treatment, tailored to the demands of wind turbine gearboxes, achieve up to four times longer rating life, featuring increased torque density and greater system reliability. In addition, this new steel and heat treatment has a higher robustness against typical failure modes in wind turbine gearboxes, thus extending the service life of the turbine.
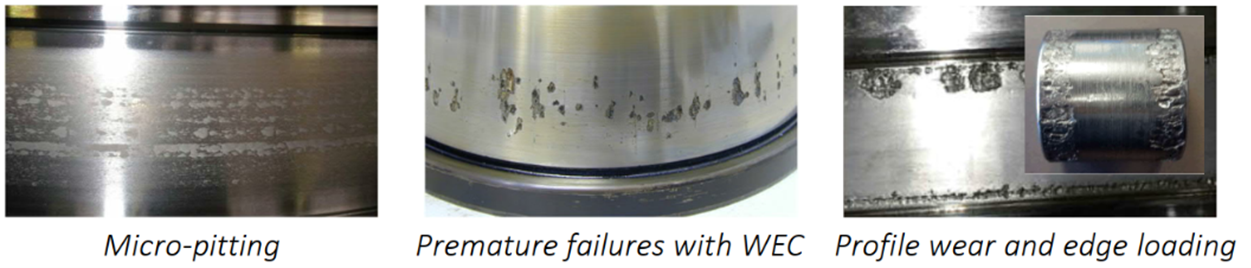
New era?
But how can this new development for one component in the gearbox make a big difference in the wind industry?
The load carrying capacity of rolling bearings is one of the main parameters determining the size of the planet gear and ring gear. Reducing the bearing size, therefore, has a direct influence on the overall gearbox dimensions, weight, and the so-called torque density (ratio between torque and gearbox weight).
Wind turbines need to become larger to reduce the levelized cost of energy. However, for transportation the size of the largest components of onshore turbines should be limited. For offshore turbines, the total weight of the drivetrain needs to be reduced to minimize the cost of main components such as the tower and foundation. The torque density is therefore a crucial factor in the race to reduce the levelized cost of energy.
Check out these sources for additional information: